Restucco & Stucco Repair
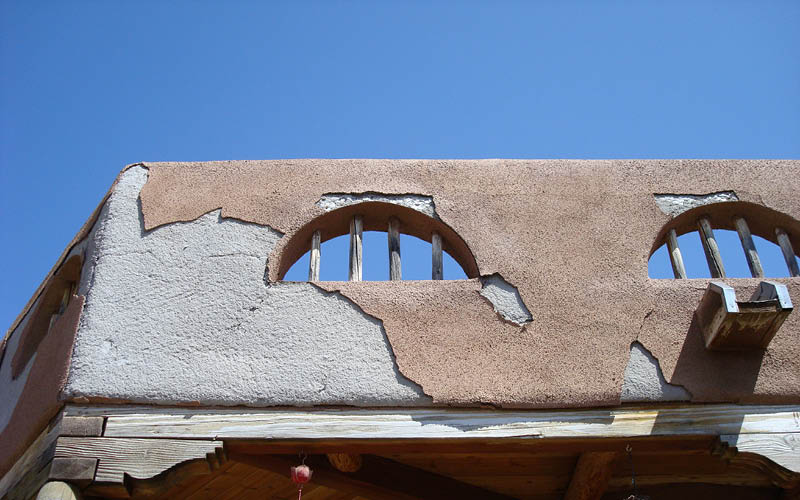
One of our most common stucco applications here in Albuquerque is that of restucco. Residential or commercial properties with damaged or tired exteriors benefit greatly from waterblasting and a new coat of color.
There is a myriad of different ways to approach a restucco project, dependent largely on the existing finish and what actions must be employed to create or promote a uniform substrate or ‘base’. Stucco is ONLY as strong as its substrate and therefore any weakness or discrepancy in any base will wreak havoc with the final color coat. This is especially true in the case of steel trowelled smooth restucco, which is not only highly susceptible to cracking, but also extremely prone to discoloration or ‘ghosting’ when applied to substrates lacking in uniformity.
Many so called ‘professionals’ will tell you that it is ok to “stucco over” an existing finish. Whilst this may be ‘theoretically’ possible with the use of a PVA bonding agent; it is without doubt the weakest method to adopt, and should be done so with extreme caution. In taking this route, one is relying COMPLETELY on the integrity of the existing finish coat.
It should be noted that the ONLY way to correctly restucco any structure with an existing stucco finish, is by utilizing the services of a professional stucco applicator such as B W Earp. Pressure washing not only removes the existing and often ‘compromised’ top coat, but also ‘opens’ up the substrate to reveal the issues often hidden underneath.
Another common form of restucco employs the need to either remove or apply wire mesh over existing wood siding. This scenario calls for a combination of restucco AND full lath stucco application. In this situation, any newly ‘opened’ or exposed areas needed to be lathed and ‘scratched’ prior to performing any kind of pressure washing. The reason for this is simple – open areas MUST be closed up to protect the subject property’s frame work from the damage that could so easily be caused by a high pressure jet of water (Pressure washing).
There are any number of hurdles that can and often do present themselves in a basic restucco project. Probably the most common of all, is the need to “tie in” new stucco with old. This may be the case when a property has existing stucco but with a new addition which will require a full lath application. Again, all ‘open’ areas MUST be closed before sandblasting can commence. The most important aspect to this case of restucco however; is the brown coat which needs to be applied over the ENTIRE structure. This is not only necessary for the full lath installation, but also serves to ‘level’ the newly cleaned areas, and thus providing a UNIFORM substrate.
It is also highly recommended to implement a fiberglass mesh wrap in any restucco situation. The additional support of the fiberglass truly works wonders in securing a uniform and durable finish.
Stucco Repair
While stucco is a popular choice among homebuilders in Albuquerque and all of New Mexico, it’s not unusual for cracks to appear at some point in your home’s lifecycle. Damage can range from hairline cracks to unsightly cracks, blemishes, and holes. In some cases, the damage is due to external conditions; in others, an accident or construction project requires stucco repairs.
BW Earp can, in many cases, restore your home’s exterior beauty. Our restoration process begins with power washing the exterior walls, repairing the stucco and finally repairing the home’s exterior trim. Often, this is all that’s needed to restore your home’s exterior to make it look as good as when it was first done.
Parapet Repair
The portion of the wall which spans above the roofline is the parapet. Because both sides of the wall are exposed to extreme temperature changes and large amounts of rain, parapets are susceptible to thermal and water-related problems. Avoiding these dangers requires careful detailing and vigilant maintenance.
The top of the parapet wall is the most vulnerable area for water-related problems to occur. Water eventually enters into the wall through the cap or through gaps in metal cap seams or brick coping at top. Continuous through-wall flashing should be installed beneath the mortar bed, directly under the cap, to prevent water from entering the wall through the joints. The flashing should extend completely through the parapet wall, with the ends bent to form a drip.
Parapet walls expand and contract at a greater rate than masonry because the parapet lacks the dead load of the masonry above to help contain movement. If this movement is not accommodated, displacement of the cap and cracks in the stucco can occur. Thermal movement should be accommodated by installing twice as many expansion joints in the parapet as the wall below. Also, installing one soft joint for every section of coping stone can prevent coping misalignment and joint failure.